LFP versus mineral-intensive batteries: a new chapter in electric vehicles (EVs)
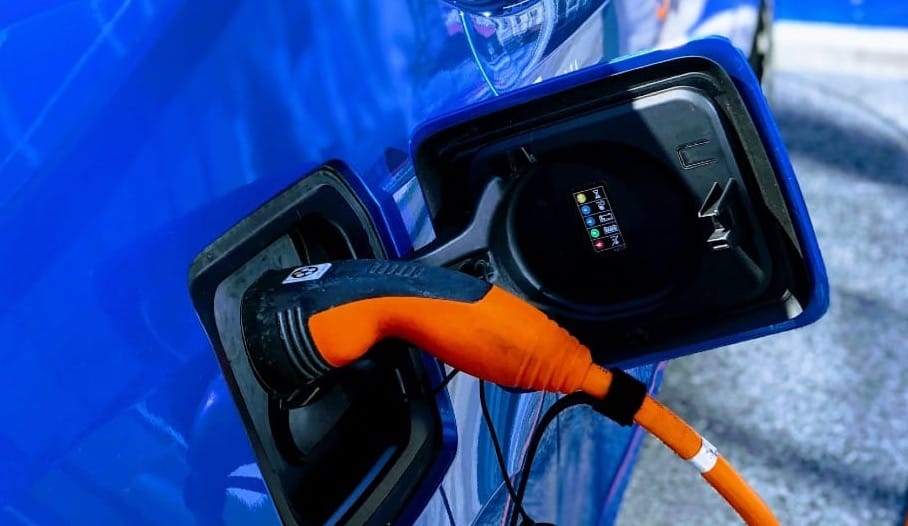
Introduction: the battery arms race in the EV era
The global transition to electric vehicles (EVs) is accelerating and so is the race to dominate battery technology.
While the spotlight has long been on nickel and cobalt heavy lithium-ion batteries, lithium iron phosphate (LFP) batteries are staging a powerful comeback. Once considered a budget option, LFPs are now reshaping battery supply chains, pricing dynamics, and even geopolitics.
In this Deep Blue League article, we’ll explore the key differences between LFP and mineral-intensive battery chemistries, break down their mineral models, dive into the underlying chemistry, and examine current market trends backed by real data.
What are LFP batteries?
LFP stands for Lithium Iron Phosphate, a type of lithium-ion battery that uses lithium, iron, and phosphate as its primary active materials.
Key characteristics:
- Chemistry: LiFePO₄ (Lithium Iron Phosphate)
- Cathode materials: Iron, phosphate
- Anode: Graphite (similar to other lithium-ion batteries)
- Energy density: 120 to 160 Wh/kg (lower than nickel-based alternatives)
- Cycle life: 2,000 to 5,000+ cycles
- Safety: Very stable; lower risk of thermal runaway
- Cost: Significantly cheaper than nickel-cobalt chemistries
The minerals model: LFP vs. NMC/NCA Batteries
Let’s compare the mineral intensity of LFP batteries with the two dominant alternatives: Nickel Manganese Cobalt (NMC) and Nickel Cobalt Aluminum (NCA) batteries.
Mineral | LFP (LiFePO₄) | NMC (e.g., NMC 811) | NCA |
---|---|---|---|
Lithium | ✓ | ✓ | ✓ |
Iron | ✓ | ✗ | ✗ |
Phosphate | ✓ | ✗ | ✗ |
Nickel | ✗ | ✓ | ✓ |
Cobalt | ✗ | ✓ | ✓ |
Manganese | ✗ | ✓ | ✗ |
Aluminum | ✗ | ✗ | ✓ |
Key implications:
- LFP batteries eliminate reliance on high-cost, high-risk minerals like cobalt and nickel, often sourced from geopolitically sensitive regions like the Democratic Republic of Congo.
- LFP production is less environmentally intensive and better suited to regionalised supply chains, particularly in China, which controls over 92% of global LFP battery production (Ufine Battery, 2024).
Why the market is pivoting to LFP
Once dismissed for lower energy density, LFP batteries are now a preferred choice for:
- Entry-level EVs
- Electric buses and commercial vehicles
- Stationary energy storage systems (ESS)
Market performance and growth
According to Benchmark Mineral Intelligence, LFP cathodes accounted for 56% of global market share in 2024, up from ~10% in 2020 (Benchmark, 2024).
Meanwhile, the International Renewable Energy Agency (IRENA) reports that LFP batteries represented about 44% of global passenger EV battery use in 2023, surging from single digits in 2015 (IRENA, 2024).
Tesla's strategic switch
In 2021, Tesla announced it would transition its standard range Model 3 and Model Y vehicles to LFP chemistry (Recurrent Auto). By 2023, over 50% of Tesla vehicles shipped used LFP batteries, significantly reducing their dependency on nickel and cobalt.
BYD’s LFP-first approach
BYD, China’s largest EV manufacturer, uses LFP almost exclusively. It surpassed 135 GWh in battery capacity by 2022 (Automotive Manufacturing Solutions) and shipped 4.14 million EVs and hybrids in 2024 (SNE Research, 2025).
Performance trade-offs: energy density vs. longevity
LFP Strengths:
- Superior thermal stability
- Longer cycle life
- Lower cost per kWh
- Simpler, more ethical supply chains
LFP limitations:
- Lower energy density (~120 to 160 Wh/kg versus 200 to 250 Wh/kg for NMC/NCA)
- Cold-weather performance can be weaker without sophisticated thermal management
That said, CATL’s Qilin battery, based on cell-to-pack (CTP) LFP architecture, now achieves up to 160 Wh/kg with higher volume efficiency—bringing LFP closer to parity with higher-density chemistries (CATL, 2022).
Chemistry in focus: how LFP works
LFP uses olivine-based phosphate chemistry (LiFePO₄) with a robust crystal structure that resists oxygen release, reducing fire risk. It offers:
- 3.2V nominal voltage
- Excellent thermal and structural stability
- Extremely low degradation across cycles
Advancements in CTP architecture, pioneered by BYD and CATL, allow manufacturers to skip modules and install battery cells directly into packs, improving energy density by 10 to 15% and cost-efficiency at scale.
Future outlook: two chemistries, one market
Rather than a winner-take-all scenario, battery markets are diverging:
- LFP for cost-sensitive, urban, and commercial vehicles
- NMC/NCA for long-range, high-performance or premium models
Meanwhile, global battery demand surpassed 1 TWh in 2024, driven by a 25% rise in EV sales, according to the International Energy Agency (IEA, 2024).
Conclusion: LFP is no longer a compromise
As EV adoption surges, LFP batteries are emerging as a critical enabler of scalable, affordable, and geopolitically safer electrification. They’re reshaping supply chains, breaking cost barriers, and challenging assumptions about what makes a battery “better.”
For anyone investing in, regulating, or innovating around EVs, understanding the nuances of battery chemistry, especially the rise of LFP, is foundational to navigating the next decade of global energy transition.